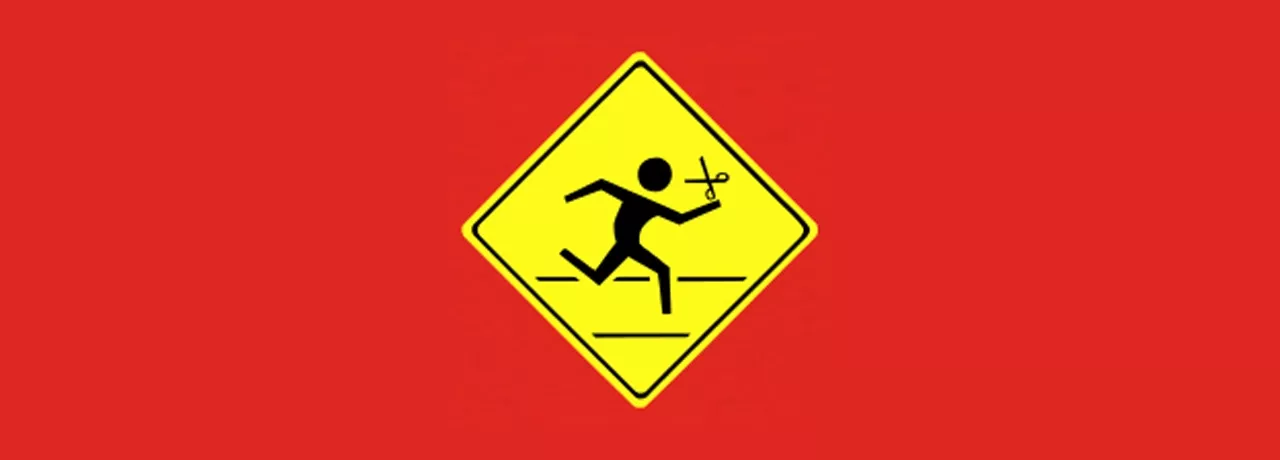
Can You Really Afford to Skip Company Safety Incentive Programs?
August 19, 2014
By Charlla Feller-Davis
Company safety incentive programs are critical to the health and safety of your organization. I learned this early on as a professional.
My first job out of college was with a small television news station in East Texas. I just happened to be on-site at a chemical plant one morning when a fiery explosion lit up the sky and triggered complete chaos. It’s not surprising that my cameraman and I were immediately escorted off the premises by a small team of very large no-nonsense men.
In the days that followed, we were able to piece together what had happened from the reticent public relations rep. It was a nightmare scenario that no company wants to happen—an unfortunate accident that has played out many more times since that day.
Yet despite horrific events, fiery explosions don’t come anywhere close to being the leading cause of workplace deaths.
The Fatal Four
While their deaths may not make the news, 12 people die every day from workplace accidents. The majority of them are caused by the fatal four:
- Falls
- Blunt force from an object
- Electrocution
- Caught between/crushed
In 2012, 4,628 workers were killed on the job in the United States, and an estimated 50,000 died from occupational diseases, resulting in a loss of 150 workers each day from hazardous working conditions. These preventable tragedies not only disable workers and devastate families, but they also damage a company’s financial well-being and take a toll on our national economy.
As important as they are, the best practices for safety don’t just happen. That’s why Congress created the Occupational Safety & Health Administration (OSHA) in 1970. Today, nothing strikes fear in the hearts of supervisors, foremen and safety managers than an unexpected OSHA inspector on-site. With an operating budget of nearly $564 million in 2013, OSHA is responsible for establishing and enforcing standards designed to protect the safety of nearly 130 million U.S. workers—a daunting task by any measure.
Empowered by legislated authority, OSHA:
- Ensures all facilities regard worker safety and health as a fundamental value
- Conducts worksite analysis of existing hazards
- Anticipates and prevents harmful occurrences
- Conducts regular site inspections
- Establishes work area procedures
- Provides safety and health orientation and training
“We all know that legislating action and implementing it in the real world are two different things—especially when employees are a major part of the equation,” says vice president of sales at Inspirus. “While attitudes about safety have grown more sophisticated—and employers are more diligent about education, training and monitoring—employees can often be a wild card without a proper safety incentive program in place.”
Depending on whether you consider “the glass half empty” or “the glass half full” might very well affect your attitude about providing employees with an added incentive (beyond their own physical well-being) to be diligent about practices that promote safety, protect lives and prevent costly accidents. Hardliners may argue, “I am NOT going to pay extra for employees to follow the rules and be safe.” Pragmatists may say, “Nothing has a way improving performance like a little incentive.”
“Regardless of where you may fall on the scale, every company is paying out money every time there is an accident. And it isn’t petty change,” says the vice president of sales.
The High Cost of Workplace Accidents
The National Safety Council shed light on the very high costs associated with workplace deaths and injuries in its 2012 report, “Injury Facts.” Analyzing data from 2010—the latest year for which information is available—the report reveals:
- The total cost of work-related deaths and injuries was nearly $177 billion. Employers spend about $1 billion per week on wage payments and medical care alone.
- The average cost per work-related injury ran $37,000. This figure does not include additional associated costs such as lost productivity, retraining, hiring new employees, administrative time, repair and replacement of equipment, etc.
- An estimated 60 million days of work were lost due to workplace death and injuries.
- A workplace injury takes place every six seconds—which equals 96,000 every week.
True, there is a cost associated with a safety program (on average about $100 per employee, per year), but it pales in comparison to the cost associated with an accident.
A 400% Return on Investment
In contrast, organizations that implement a leading-indicator company safety incentive program see several tangible benefits. “Research tells us that each dollar an employer invests in a health and safety plan can save a company $4 to $6,” says Floyd. “That means the minimum return on investment an employer can expect from creating a well-defined safety program and culture is 400%.”
But for many companies that successfully leverage the power of a company safety incentive program, the results have been much more dramatic:
- Heartland Foods went from 285 lost-time injuries per year to just 14—saving $11,653,000 in the process.
- Allied Waste has seen a 27% decline in safety-related accidents, reduced claims by 2,520 and saved more than $108 million as a result.
- Airgas East/Northeast spent $181,500 on their safety incentive program but saved $907,500 in one year.
Along with reducing accidents, protecting workers, and lowering workers’ compensation costs and legal penalties, there’s another big bonus: Safety incentive programs boost employee morale, productivity and retention. With results like these, it’s hard not to imagine the very tangible difference a safety incentive program could make in your organization. As a pragmatist might say, “Can you really afford not to implement one?”
Melissa Gatchel-North is a national Emmy-nominated and award-winning writer who has profiled some of the nation’s most interesting companies and their maverick founders—including FUBU, Hard Candy Cosmetics, Human Genome Sciences and many others.